TM
Manufacturing Process
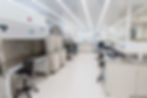
GMP Manufacturing Facility
The current Good Manufacturing Practice (cGMP) islet manufacturing facility is located at UI Health in Chicago, IL. Lantidra is manufactured in this facility under aseptic processing conditions consistent with U.S. FDA regulatory standards.
​
Manufacturing and support operations (approx. 2,250 square feet) consist of classified areas (International Organization for Standardization ISO 7 and ISO 8) with ISO 5 Biological Safety Cabinets (BSCs) and Controlled Not Classified (CNC) areas.
​
​
Islets are sourced from the pancreas of a deceased donor. Donor pancreas allocation to the intended recipient occurs through UNOS, and organ procurement is handled by an organ procurement organization (OPO) and the transplant center’s transplant surgeons. The manufacture of purified pancreatic islets from the eligible donor pancreas is a complex process with multiple manufacturing steps. Once the pancreas is procured, delivered, and accepted for processing at the facility, all manufacturing steps involving the pancreas and pancreatic tissue are performed in certified ISO 5 BSCs in the ISO 7 classified area using aseptic processing techniques. The manufacturing process is continuous from the time the donor organ is received through the release of the final drug product (Lantidra; donislecel).

The islet isolation process is broken down into drug substance manufacturing steps (pre-islet culture) and drug product manufacturing steps (post-islet culture). A flow diagram of the principal steps in the overall manufacturing process are provided in the figure below. Each Lantidra lot consists of islets isolated from a single donor pancreas intended for a single designated islet recipient. The donor pancreas is considered incoming raw material and is screened and qualified prior to acceptance. Due to the nature of Lantidra and its intended use, there is always a batch size of one unit. Quality Control (QC) testing of Lantidra is performed prior to release.
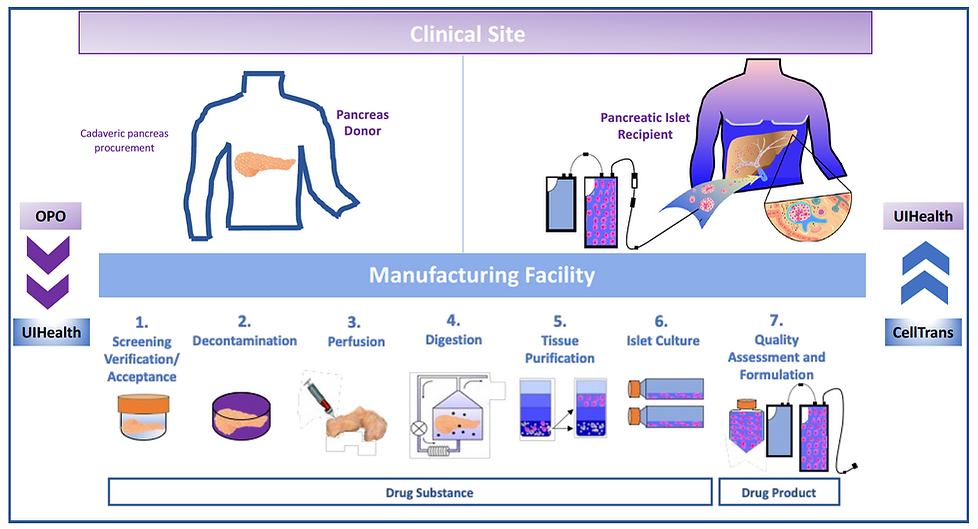